Results
Comparing the mass flow through the tiles shows quite a big difference if a porous medium tile is used which is directly connected to the server room or if the raised floor plenum is modelled separately from the server room.
If the raised floor plenum is modelled separately a good match is found in mass flow behaviour through each of the tiles compared to the paper. The middle tile gets the highest mass flow. Whereas the mass flow decreases when moving to the tiles closer to the CRA/C units. However, when modelling the tiles as a porous medium in between the raised floor plenum and the server room it is visualized that the mass flow through each of the tiles is constant. This indicates that the resistance produced due to the tile perforation has a much higher influence on the distribution of the mass flow through the tiles than the location of the tile with respect to the CRA/C unit.
This result indicates that the assumption made in the previous article, where each tile had a constant mass flow into the server room, is correct.
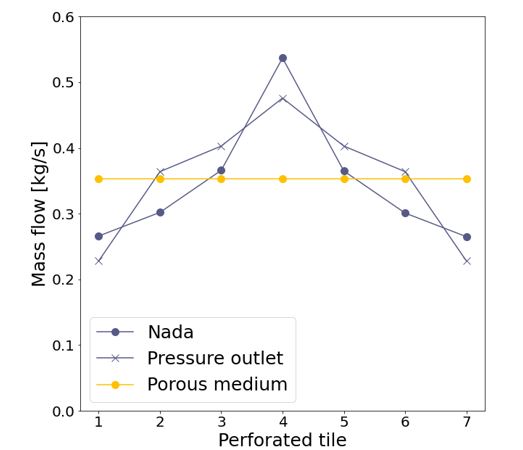
Figure 2: comparison in mass flow
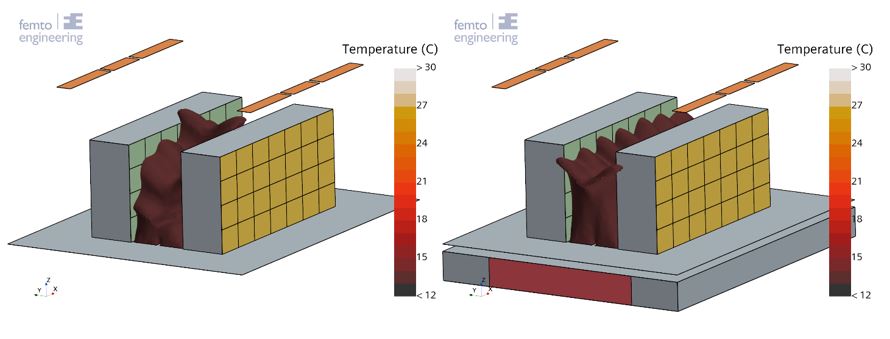
Figure 3: Isosurface at 13C; left: separate simulations, right: single simulation
In Figure 3 a comparison is drawn between the temperature isosurface for 13C. On the left the isosurface is shown for the simulation where first the area below the raised floor is run and then the simulation for the server area. On the right the isosurface is shown for the same simulation but now the entire data center is simulated in one go. It is visible that the isosurface on the left shows the same curve as was shown in the graph, Figure 2. The isosurface on the right however shows a wave-like behaviour. Where a lower temperature reaches a higher location where the tiles blow cold air into the server room, and the temperature rises slightly between the tiles.
The more constant distribution of temperature over all server racks in the simulation where a constant inflow through the perforated tiles is present compared to the simulation where the inflow through the tiles increases towards the middle of the server racks is shown in Figure 4. The simulation where only the server room is simulated has the highest temperature at 29.7C in the hot aisle top corners of the two rack rows (as shown in Figure 5a). The maximum temperature in the simulation of the full data center is a full degree lower at 28.7C. This temperature is located at the top corners of the middle server rack, as shown in Figure 5b.
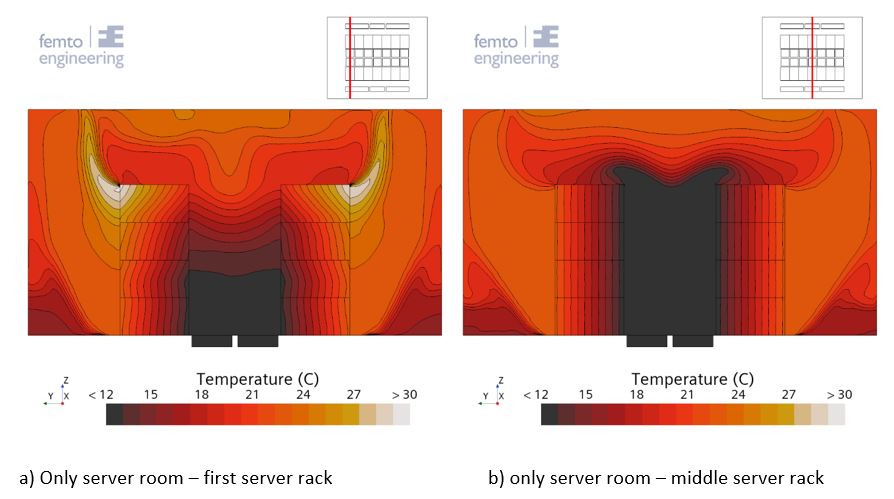
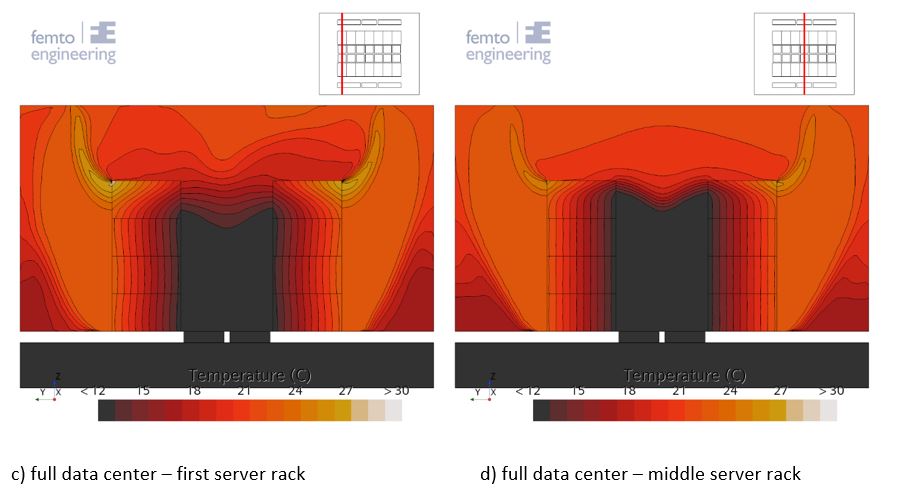
Figure 4: rack temperature distribution comparison
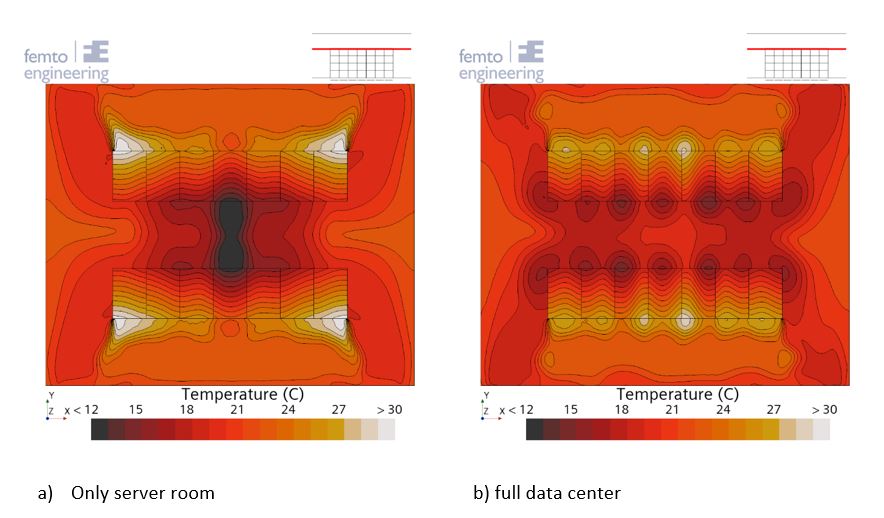
Figure 5: temperature distribution at Z = 1.95m